Impact of Transformer Core Manufacturing on the Environment
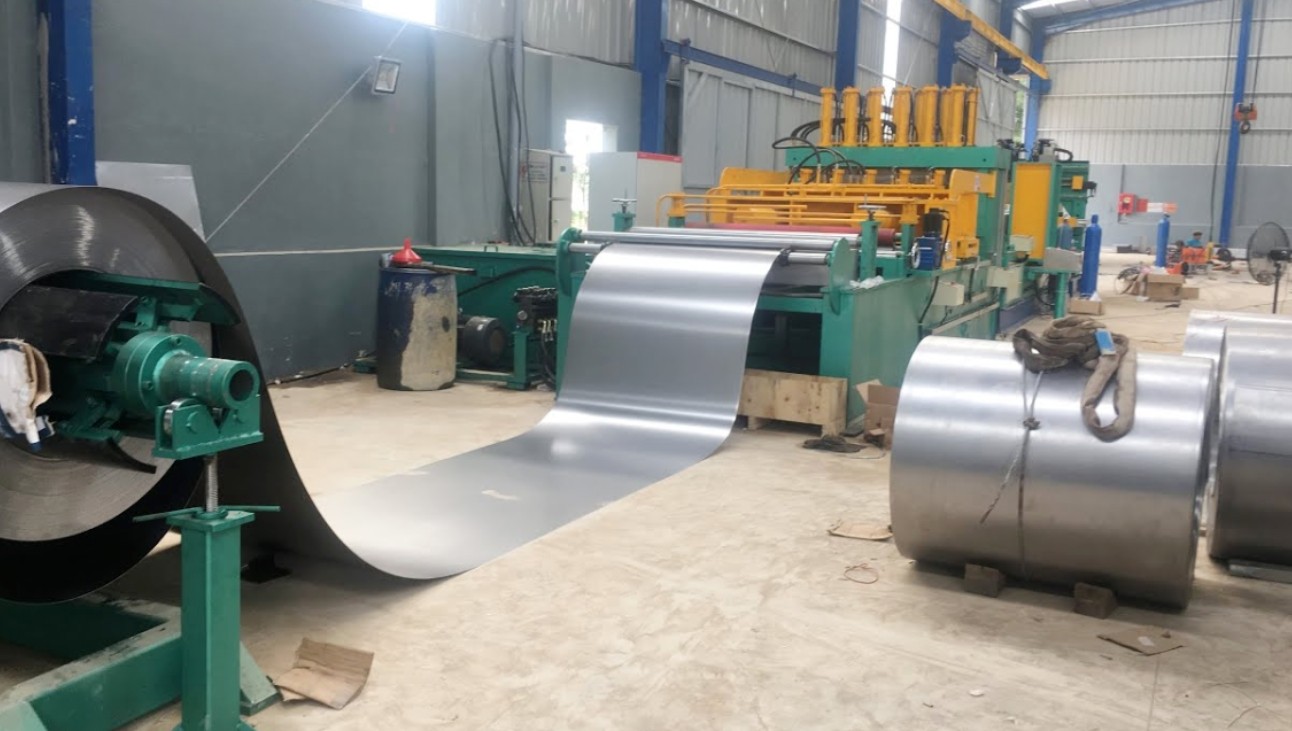
Transformers are an important component in power systems, enabling efficient transmission and distribution of power. The heart of every transformer is its magnetic core, which plays a fundamental role in its performance. However, the manufacturing process of transformer cores can have significant environmental impacts. In this article, we explore the environmental impacts of transformer core manufacturing and potential mitigation measures.
What Is a Transformer Core Production Line?
The transformer core production line is a manufacturing process specially designed for the efficient production of transformer cores. It involves a series of interrelated steps and machinery that transform raw materials into finished transformer core components. The production line usually starts with the selection and processing of raw materials, such as silicon steel or amorphous metal alloys, which have the required magnetic properties for the transformer core. These materials are then cut, stamped, or formed into the required size using specialized equipment.
Once the core materials are ready, they undergo a stacking and assembly process in which individual laminations or sheets are layered together to form the core structure. At this stage, precision is critical to ensure correct alignment and minimal magnetic losses. After assembly, the core may undergo an annealing or heat treatment process to relieve internal stress and enhance magnetic performance. Quality control measures are implemented throughout the production line to verify dimensions, magnetic properties, and overall performance.
Transformer core production lines may also include additional surface treatment, insulating coating, and final inspection stages before the finished core is packaged and shipped to the transformer manufacturer or assembly plant.
Transformer Core Manufacturing Process
Material Selection and Preparation:
- The manufacturing process begins with the careful selection of raw materials suitable for the transformer core. The most commonly used materials include silicon steel and amorphous metal alloys, chosen for their magnetic properties and ability to minimize energy loss.
- Silicon steel, also known as electrical steel, is favored for its high magnetic permeability and low core losses. It goes through a series of processing steps such as rolling, annealing, and insulating coating to achieve the required magnetic properties and electrical insulation.
- Amorphous metal alloys have lower core losses than silicon steel but require specialized manufacturing techniques (such as rapid solidification) to maintain their amorphous structure.
- Once the materials have been selected and processed, they are cut to precise shapes and sizes using shears or laser cutting technology, ready for the core assembly stage.
Core Assembly and Stacking:
- The core assembly process involves stacking individual laminations or processing sheets of material to form the core structure. Each lamination is coated with insulation to prevent electrical losses and minimize eddy currents.
- During the core stacking process, precision is critical to ensure uniformity and minimize air gaps between laminations, which otherwise result in increased core losses and reduced efficiency.
- Use specialized stacking machines or manual assembly techniques to arrange the laminations in a specific order, alternating between layers to reduce flux leakage and improve core performance.
- Once the core is fully stacked, it is compressed, bonding the laminations together and eliminating any remaining air gaps. Use a hydraulic press or mechanical clamps to apply even pressure across the core surface to ensure structural integrity and optimal magnetic coupling.
- The assembled core may undergo additional processes such as heat treatment or surface finishing before being checked for quality and performance parameters.
Environmental Impact of Transformer Core Manufacturing
Energy Consumption: The manufacturing process of transformer core requires a lot of energy, especially in the production of important raw materials such as silicon steel or amorphous metal alloys. Energy-intensive stages such as steel manufacturing, rolling, annealing, and insulating coating significantly increase electricity consumption and carbon emissions. Additionally, reliance on fossil fuels for electricity generation exacerbates environmental impacts, leading to rising greenhouse gas emissions and exacerbating concerns about climate change. These cumulative factors highlight the urgent need for sustainable alternatives and energy-saving practices in the transformer core manufacturing industry to mitigate its adverse environmental footprint.
Emissions: Transformer core manufacturing emits pollutants throughout the production chain, with the burning of fossil fuels for power generation being a major source. This process releases carbon dioxide (CO2), sulfur dioxide (SO2), and nitrogen oxides (NOx) into the atmosphere, causing air pollution and respiratory disease. In addition, emissions from steel production, including activities such as smelting and casting, emit particulate matter and greenhouse gases that contribute to global warming and environmental degradation. These combined emissions highlight the urgent need for strict environmental regulations and sustainable practices to mitigate the adverse impacts of transformer core manufacturing on local and global ecosystems.
Waste Generation: During the transformer core manufacturing process, waste is generated at multiple stages including scrap steel, insulating coating by-products, and packaging materials. Improper disposal of these wastes poses significant environmental risks, including contamination, soil degradation, and ecosystem damage. To address these challenges, minimizing waste generation and adopting recycling and reuse strategies become key measures. By doing so, the environmental impact of transformer core manufacturing can be mitigated while increasing resource efficiency and adhering to circular economy principles.
In Conclusion
The environmental impact of transformer core manufacturing highlights the need for sustainable solutions and responsible practices. By prioritizing energy efficiency, emissions reduction, and waste minimization, the industry can reduce its environmental footprint and contribute to a more sustainable future. If you want to purchase a transformer core production line, please contact us.
Hengli is a professional transformer core production line manufacturer and supplier, providing cutting-edge solutions for efficient, high-quality core manufacturing. Hengli's production lines are dedicated to innovation and reliability, using advanced technology and precision engineering to streamline the manufacturing process. From material selection and preparation to core assembly and stacking, Hengli's production lines ensure optimal performance and productivity while adhering to strict quality standards. Whether it is silicon steel or amorphous metal alloys, Hengli can provide tailor-made solutions to meet the diverse needs of global transformer manufacturers. Hengli's reputation for excellence and focus on customer satisfaction have made Hengli a trusted partner in the transformer core manufacturing industry, providing comprehensive support and expertise every step of the way.