How to Improve the Efficiency of Transformer Core Production Line
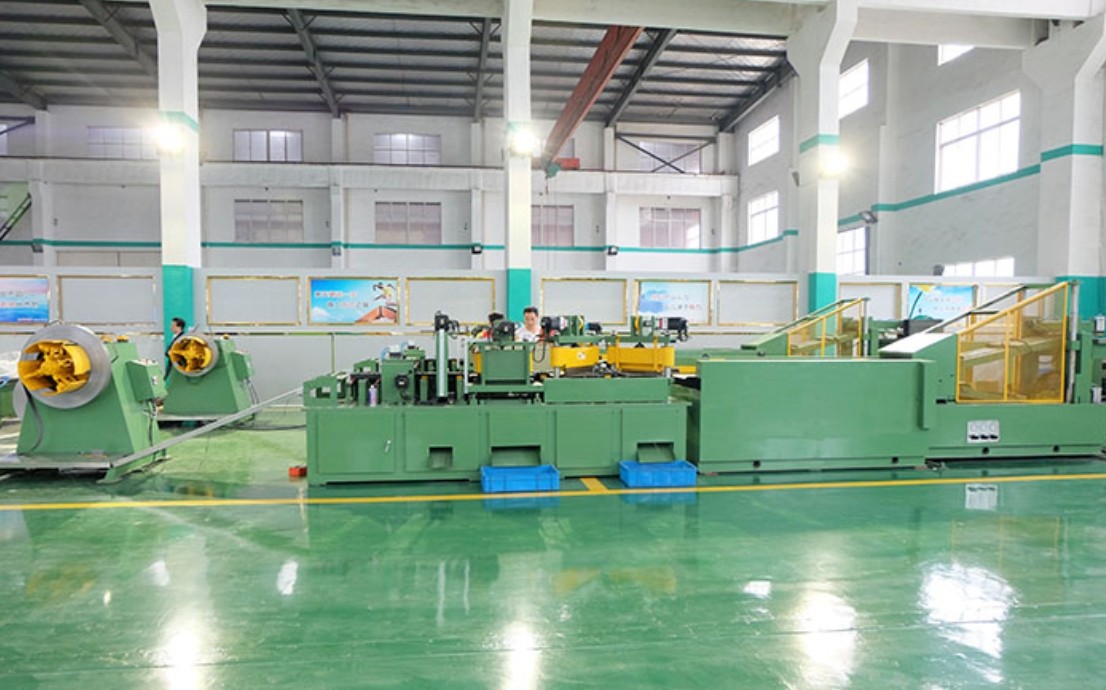
The efficiency of transformer core production lines is of paramount importance as they are the backbone of power transformers and are vital in ensuring a seamless power transmission and distribution network. Optimizing the efficiency of these production lines is important, not only to meet production targets but also to effectively manage operating costs and remain competitive in the market. In this article, we will explore strategies and techniques for improving the efficiency of transformer core production lines.
Tips to Improve the Efficiency of Transformer Core Production Line
Simplified Workflows and Process Optimization: Optimizing workflows and processes within the transformer core production line is critical to improving efficiency. Manufacturers should conduct a thorough assessment of existing processes to identify bottlenecks, redundancies, and areas for improvement. By streamlining workflows and eliminating non-value-added activities, such as unnecessary material handling or redundant inspections, manufacturers can minimize lead times, reduce waste, and increase overall throughput.
Invest in Advanced Machinery and Technology: Investment in advanced machinery and technology is critical to modernizing and improving the efficiency of transformer core production lines. Manufacturers should explore the latest advances in automation, robotics, and digital manufacturing solutions to optimize production processes. Automated machinery can perform repetitive tasks accurately and consistently, reducing the need for physical labor and minimizing the risk of errors.
Employee Training and Skills Development: Investing in employee training and skills development is critical to optimizing the efficiency of your transformer core production line. Well-trained, knowledgeable workers are critical to operating machines efficiently, solving problems, and implementing continuous improvement programs. Manufacturers should provide comprehensive training programs to equip employees with the necessary technical skills, safety protocols, and quality standards required for their roles. Additionally, fostering a culture of continuous learning and empowerment encourages employees to contribute innovative ideas and actively participate in process improvement activities. By investing in the professional development of their employees, manufacturers can build a highly skilled and motivated team capable of driving efficiency gains and achieving operational excellence.
Common Challenges in Transformer Core Production
In transformer core production, manufacturers encounter various challenges that can affect efficiency and productivity. A common challenge is the complexity of the production process, which involves multiple complex steps such as cutting, stacking, welding, and testing of core laminations and components. Coordinating these processes while maintaining accuracy and quality standards can be a difficult task and prone to errors, leading to production delays and increased costs.
Another challenge is the need for specialized equipment and skilled labor, which can be costly to acquire and train. In addition, ensuring consistent material quality and availability poses significant challenges, as variations in raw materials can affect the performance and reliability of the transformer core. In addition, stringent industry regulations and standards add further complexity, requiring manufacturers to adhere to strict guidelines and undergo rigorous testing and certification processes. Meeting these challenges requires careful planning, investment in technology and training, and ongoing process optimization to ensure efficient and reliable transformer core production.
In Conclusion
Improving the efficiency of transformer core production lines is critical to meeting the growing demand for reliable power infrastructure. By adopting innovative technologies, optimizing processes, and investing in employee development, manufacturers can increase productivity, reduce costs, and stay ahead of the rapidly evolving market landscape. If you are looking for a reliable transformer core production line manufacturer, please contact us.
Hengli is a professional transformer core production line manufacturer. It is a national high-tech enterprise specializing in the R&D and manufacturing of high-end industrial automation equipment. We want to provide the right solution, one that is tailored to your specific business realities. We will listen carefully to your requirements and work with you to identify all aspects that need to be addressed, including materials, work, operator, and packaging considerations. We specialize in providing reliable machines that increase your productivity, reduce waste, and improve output quality.
Frequently Asked Questions
What are the benefits of automation for transformer core production lines? Automation can benefit transformer core production lines by streamlining operations, reducing manual labor, and increasing productivity. Automated machinery can perform repetitive tasks accurately and consistently, minimizing errors and increasing throughput. Additionally, automation enables manufacturers to optimize resource utilization, reduce production costs, and increase overall efficiency.
What role does quality control play in improving efficiency? Quality control plays a vital role in improving efficiency by ensuring that products comply with predefined standards and specifications. By implementing robust quality control measures, manufacturers can detect defects early in the production process, minimize rework and scrap, and maintain consistent product quality. This reduces production delays, increases customer satisfaction, and improves overall efficiency.
Can lean manufacturing principles be applied to small-scale production lines? Yes, lean manufacturing principles can be applied to small-scale production lines. The core principles of lean manufacturing, such as waste reduction, continuous improvement, and value stream mapping, apply to businesses of all sizes. By adopting lean practices, small manufacturers can streamline processes, optimize resource utilization, and increase efficiency, ultimately increasing competitiveness and profitability.
How can IoT integration improve the real-time monitoring of production facilities? IoT integration enables real-time monitoring of equipment and processes in production facilities by connecting sensors and devices to centralized monitoring systems. IoT-enabled sensors collect data on various parameters such as temperature, pressure, and machine performance, allowing operators to monitor operations remotely and identify potential issues before they escalate. Real-time monitoring helps proactive maintenance, reduces downtime, and improves overall operational efficiency.
What are the main challenges in implementing efficiency improvements? Implementing efficiency improvements in a production line can present several challenges, including resistance to change, lack of employee support, and limited financial resources. Employees who are accustomed to existing processes and unwilling to embrace new technologies or methods may resist change. Involving employees in the improvement process and providing adequate training and support can help overcome resistance. Additionally, limited financial resources may limit investment in new technologies or process improvements. Prioritizing initiatives based on potential return on investment and pursuing external funding or partnerships can help address resource constraints and promote efficiencies.