Overcoming Challenges in Silicon Steel Shear Line Manufacturing
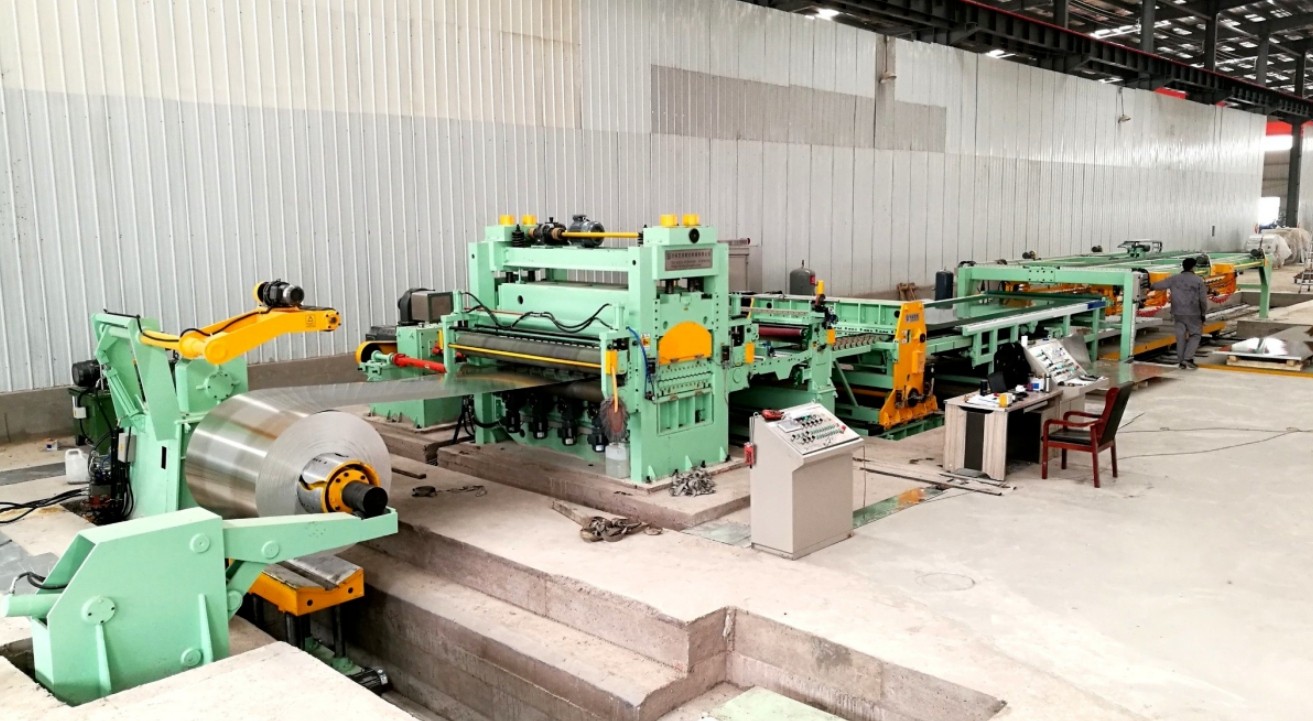
Silicon steel shear line fabrication involves the precise cutting and machining of electrical steel sheets to make laminations for transformers, motors, and generators. However, various challenges can arise along the way, affecting productivity, quality, and overall efficiency. In this paper, we delve into these challenges and explore effective strategies to overcome them.
Understanding Silicon Steel Shearing Line Manufacturing
Silicon steel shear line manufacturing is a complex process involving multiple stages, including uncoiling, leveling, cutting, stacking, and shearing of electrical steel sheets. The goal is to produce laminations of exact size and shape with a minimum of waste. These laminations are then assembled to form the core of electrical devices, ensuring efficient energy conversion.
Challenges Faced by Silicon Steel Shear Line Manufacturing
1. High Rejection Rate
One of the main challenges of silicon steel shear line manufacturing is the high scrap rate. Since laminations are cut and formed with precision, any inaccuracies can lead to wasted material. High scrap rates not only lead to increased production costs but also have an impact on the environment.
2. Precision Cutting
Precision cutting is essential for silicon steel shear wire fabrication to achieve the required dimensions and minimize material waste. However, achieving consistent precision throughout the cut can be challenging due to factors such as blade wear, machine alignment, and material variations.
3. Material Handling
Efficient material handling is critical to maintaining a smooth production flow on a shearing line. Large and heavy steel plates require proper handling techniques to prevent damage and ensure accurate positioning during cutting and stacking. Improper handling of materials can lead to errors, delays, and lost productivity.
4. Machine Shutdown
Machine downtime is a significant obstacle to silicon steel shear line manufacturing. Mechanical failures, maintenance requirements, and tool changes can cause unexpected interruptions in the production process. Minimizing machine downtime is critical to maximizing productivity and meeting production goals.
5. Quality Control
Consistent quality throughout the manufacturing process is critical to delivering reliable, efficient electrical equipment. Quality control challenges in silicon steel shear line manufacturing include detecting defects, monitoring dimensional accuracy, and ensuring lamination uniformity. Inadequate quality control measures can lead to product failure and customer dissatisfaction.
6. Environmental Issues
The manufacture of silicon steel shear lines has an impact on the environment due to waste generation, energy consumption, and potential emissions. It is critical for manufacturers to adopt sustainable practices that minimize waste, energy use, and environmental impact.
Overcoming Challenges
1. Improve Scrap Rate
To reduce scrap rates, manufacturers can employ advanced cutting techniques and precision measuring systems. Using a laser cutting machine with a real-time monitoring and control system can achieve precise cutting and minimize material waste. Additionally, optimizing nesting algorithms to increase material utilization and implementing proactive maintenance can further improve scrap rates.
2. Improve Cutting Accuracy
Regular maintenance of cutting tools, such as sharpening or changing blades, ensures consistent precision. Implementing an automated blade wear detection system can provide timely alerts for blade replacement. Advanced computer numerical control (CNC) systems can also improve cutting accuracy by compensating for material variations and machine misalignment.
3. Simplify Material Handling
Investing in automated material handling systems, such as robotic arms or conveyor belts, can reduce human error and increase efficiency. Using barcode or RFID systems to track and identify steel plates can simplify material handling operations. Proper training of operators in handling techniques can also help increase productivity and reduce errors.
4. Minimize Machine Downtime
Implementing preventive maintenance programs, predictive maintenance technologies, and condition monitoring systems can minimize machine downtime. Regularly inspecting, lubricating and calibrating machines can help identify potential problems and prevent unexpected breakdowns. Additionally, maintaining an inventory of spare parts ensures quick replacement and minimizes downtime.
5. Implement Effective Quality Control
Enhance quality control with advanced inspection technologies such as computer vision systems and non-destructive testing methods. Real-time monitoring of dimensional accuracy and lamination uniformity ensures compliance with specifications. Implementing statistical process control techniques and a comprehensive quality assurance program also contributes to consistent product quality.
6. Address Environmental Issues
Manufacturers can employ sustainable practices to reduce the environmental impact of silicon steel shear line manufacturing. This includes optimizing energy use through efficient equipment, recycling waste, and implementing pollution control measures. Compliance with environmental regulations and certifications further demonstrates a commitment to sustainable manufacturing.
In Conclusion
Silicon steel shear line manufacturing faces several challenges that can affect productivity and quality. By effectively understanding and addressing these challenges, manufacturers can optimize their processes and improve overall performance. By implementing advanced technologies, simplifying material handling, and prioritizing quality control and sustainability, manufacturers can overcome these challenges and succeed in the field of silicon steel shear line manufacturing. If you want to know more about silicon steel shearing lines or want to buy silicon steel shearing lines, please contact us.
Hengli is a professional custom silicon steel shearing line equipment manufacturer in China. Relying on modern industrial concepts and excellent automation technology, our main products include an automatic system for stamping and forming of automobile outer panels, online robots, high-precision sheet metal automatic shearing devices, industrial automatic online detection systems, electric power automation devices, and automatic control systems. Overall solution. The main products are synchronized with the world's advanced technology and are widely used in the pillar industries of the national economy such as automobile manufacturing and parts processing, steel and metallurgical processing, electric power, and metal packaging.