8 Ways to Keep Your Shear Machines in Top Condition
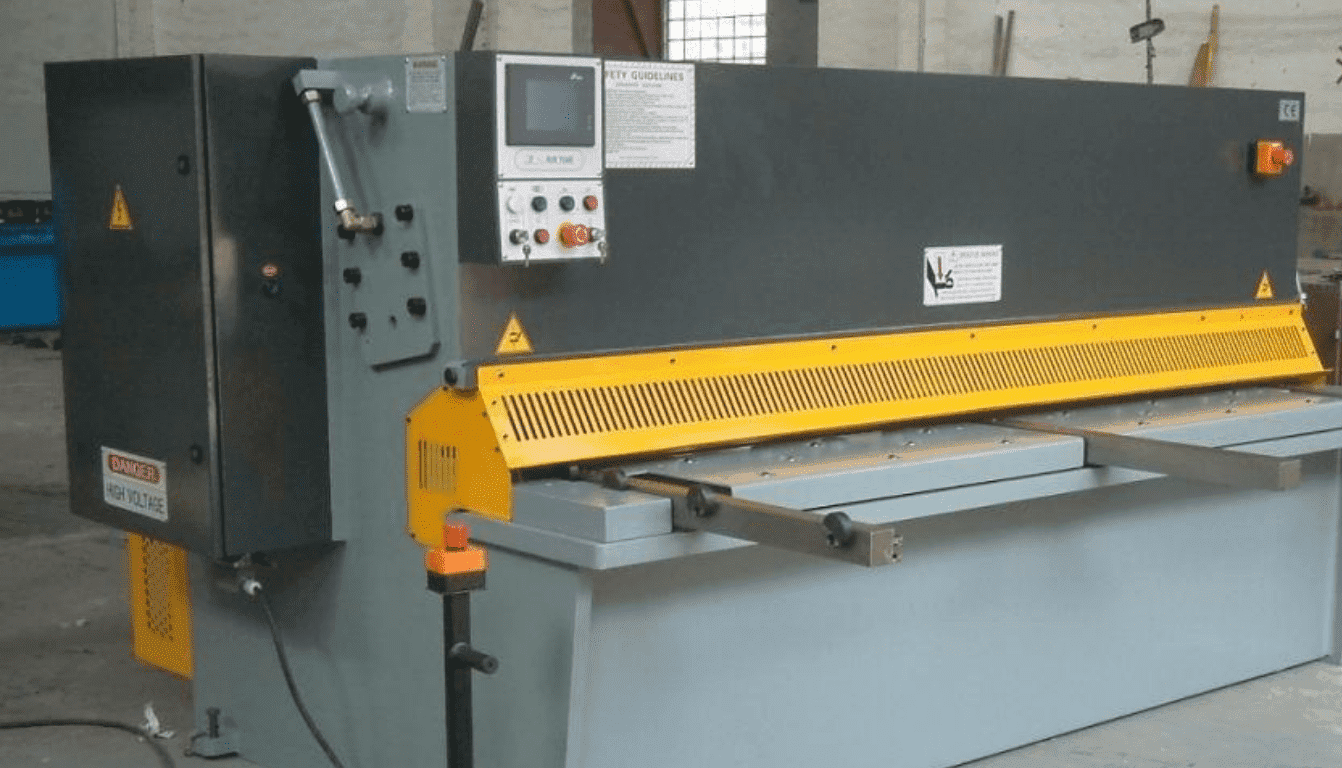
Shears machines are common manufacturing equipment found in many metal-forming plants. From small manufacturers to large factories, shears are one of the most critical and diverse tools used in metal fabrication. This article introduces 8 ways to keep your shearing machine in top condition, and I hope it can help you.
1. Know your machine
It is important to understand the function, design, and operation of the machine. The main cause of shear device failure is overloading beyond the instructions for use. Scissors are designed to cut metal of a given thickness and width.
When these limits are exceeded, corruption occurs. In addition to following the load recommendations in the instructions for use, normal adjustments should be made on a regular basis, and maintenance schedules and service requirements should be carefully followed.
Misuse of lubricants and other fluids can also cause damage. Lubricants and fluids must be used in accordance with the instructions for use.
2. Perform and document periodic inspections.
A strict inspection schedule should be posted and followed. Areas that should be checked include the shearing machine's ability to perform all operational functions; on mechanical machines, all bearings should be checked for idling and wear; and all emergency and safety functions should be checked.
3. View documentation
Data should be systematically reviewed after periodic inspection and documentation. This review can reveal wear patterns, accident potential, and nonconformities for repairs.
Documentation and analysis are the basis of preventive maintenance. Armed with this information, a clear maintenance schedule can be developed that eliminates most emergency repairs.
4. Set the blade correctly
Proper setting of shear blades is the key to extending blade and machine life. Proper clearance for blade cuts can affect the driver, plunger, tool, and cut quality. Also, before setting the blade, check the flatness of the blade seat and make sure the tool is properly seated to eliminate blade chipping caused by shifting during cutting.
If the gap is too tight, the cutting action will be incorrect due to the metal getting stuck between the blade and the machine. If the blades don't have a gap, they will break. When the clearance is too loose, the blade acts like a hammer, applying multiple forces to machine components, causing premature wear and failure.
5. Maintain the correct bead clearance.
Setting and maintaining proper bead clearance increases tool life and machine uptime. The lugs maintain the correct guiding action of the plunger and additional tools. If the clearance is not maintained, the same problem occurs when the blade clearance is ignored.
6. Isolate and level the machine
Leveling the shear and isolating it from vibration is critical to proper operation. Proper selection and installation of isolation pads can increase tool life and shear rates, reduce vibration, improve foundation life, reduce noise, and eliminate shear frame deformation.
With today's isolators, machine leveling can be accomplished in less than half an hour. Make sure the shears are level to eliminate the twisting action that could damage the shears.
7. Follow a basic maintenance schedule
The following parts of the shearing machine require regular maintenance:
1. The air system should be properly maintained to ensure clean air. All regulators must be set up for proper operation. Maintaining the regulator helps the pneumatic mechanism work properly.
2. The lubrication system must be cleaned, primed, and properly filtered. Broken, kinked, or twisted wires must be replaced. Every point must be disconnected and checked to determine if the lubrication is reaching its destination. The oil sump and water tank should be emptied, cleaned, and refilled regularly.
3. Machine clutches and brakes must be inspected for proper lining thickness, clearance, and signs of failure. Worn linings must be replaced immediately. Overtravel beyond the machine manufacturer's specifications must be adjusted and/or corrected after inspection.
4. Balance cylinders should be tested and reworked at the first sign of air leak or failure. Properly acting balancing cylinders ensure the longevity of all working parts of the shearing machine and its tools.
8. Repair as soon as possible
When damage, wear, or misalignment is found, the shears should be repaired or adjusted immediately. Most catastrophic failures are caused by delaying simple repairs. Fixing repairs quickly is almost always less expensive than correcting the damage that may have occurred by neglecting or delaying repairs. In addition, operator safety depends on timely repairs.
By performing these simple tasks, the productivity of the shearing machine can be maintained. If your shears are properly maintained, replacement costs and catastrophic failures can be avoided. Hengli specializes in making high-quality shears, if you need them, please contact us.
As a professional custom industrial automation equipment manufacturer, Hengli specializes in the production of automotive outer panel stamping and forming automation systems, online robots, high-precision sheet metal automatic shearing devices, industrial automation online inspection systems, etc. Our industrial automation equipment widely used in automobile manufacturing and parts processing, iron and steel metallurgy processing, electric power, metal packaging, and other pillar industries of the national economy.