Duplex Slitter Burst Troubleshooting: Expert Tips for Optimal Performance
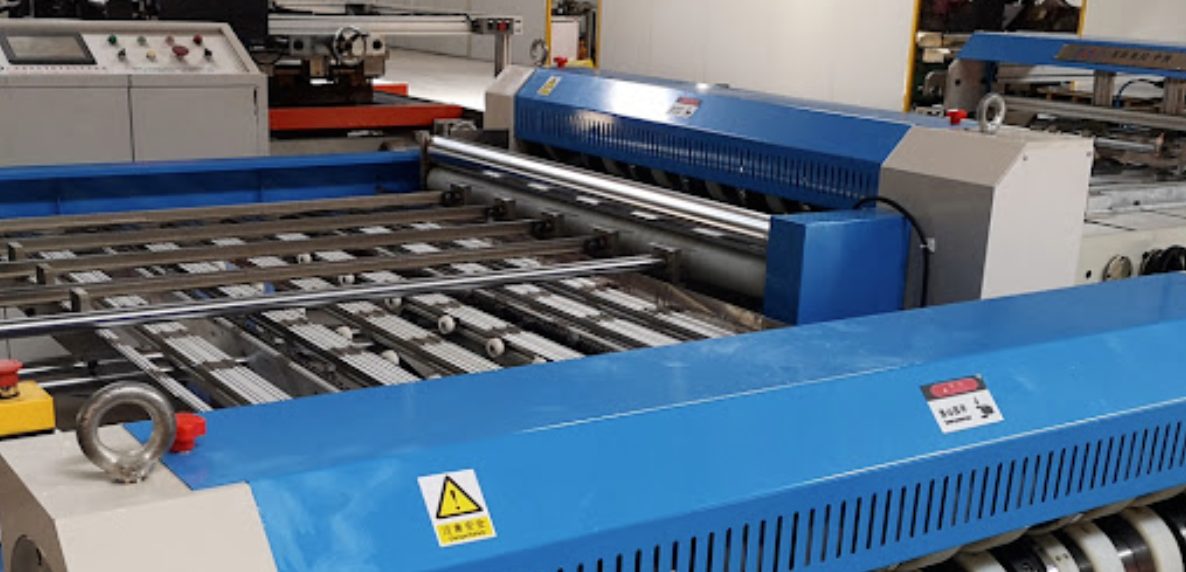
In the high-stakes world of industrial slitting, maintaining the optimal performance of your duplex slitter is critical to ensuring product quality, minimizing downtime, and maximizing profitability. At Hengli, we understand the complexities of slitter operations, especially when faced with burst issues that can severely impact your production line. This guide provides expert troubleshooting tips to help you diagnose, prevent, and resolve duplex slitter burst issues, allowing your team to operate at peak efficiency.
Understand the Causes of Duplex Slitter Bursts
Duplex slitter bursts are a common and complex problem that can be caused by a variety of factors. In order to effectively troubleshoot, it is important to understand their root causes:
1. Blade related issues
Blade-related issues are a common cause of bursts in slitting operations. Over time, blades can become dull or damaged, resulting in uneven cuts that put excessive pressure on the material, increasing the risk of bursts. Additionally, incorrect blade gap settings can result in excessive cutting pressure, which can cause the material to tear. Misaligned blades can create uneven cutting forces, further exacerbating the problem and causing weak spots in the material that are particularly susceptible to breaking.
2. Material properties and handling
Material-related factors play a crucial role in the slitting process and can significantly affect product quality. Inconsistent material tension on the roll can lead to uneven stress distribution, which increases the possibility of bursting. Variations in material thickness and hardness also require precise machine adjustments; any mismatch can apply excessive force to the blade, affecting the cutting effect. In addition, material defects such as impurities or inconsistent thickness can also affect the smooth slitting process, causing irregularities and even possible bursting.
3. Machine setup and maintenance
Improper machine setup and poor maintenance can seriously cause bursting during the slitting process. Incorrect settings (such as improper pressure, speed or tension adjustment) can create unstable cutting conditions, increasing the risk of material damage. In addition, worn or faulty parts such as bearings, rollers or tension controllers can cause unstable machine operation, which can interfere with slitting operations. Lack of regular maintenance, such as failure to remove debris or ensure good lubrication, can further compromise the machine's accuracy and overall performance.
4. Operating conditions and environmental factors
Operating conditions and environmental factors can have a significant impact on the slitting process. Running a machine at speeds beyond its designed capacity can overstress the equipment and material, increasing the risk of blowouts. Temperature fluctuations can change the physical properties of the material, affecting the stability of mechanical components and leading to erratic performance. Additionally, external vibrations or shocks can affect the precision of the slitting process, causing misalignment and potentially creating defects in the final product.
Step-by-Step Troubleshooting Procedures for Double-Sided Slitter Blowout Issues
1. Perform a thorough visual inspection
Begin by inspecting blade condition, alignment, and gap. Watch for signs of dullness, nicks, or misalignment. Inspect rollers and tensioning systems for wear or damage. Ensure that the material roll is properly positioned and that tension is even across the width.
2. Verify and adjust blade settings
- Blade sharpness: If the blade is dull or damaged, replace or sharpen it.
- Blade gap: Set the gap based on the material specification, typically between 0.1 mm and 0.3 mm for most materials.
- Blade alignment: Use a precision alignment tool to ensure the blades are parallel and centered.
3. Optimize material tension and handling
Use a tension control system to maintain consistent tension across the material width.
Adjust tension parameters based on material type and thickness.
Check for any material defects and remove damaged sections before slitting.
4. Fine-tune machine settings
Pressure adjustment: Calibrate pressure on the blade to balance cutting forces without overstressing the material.
Speed control: Operate within the recommended speed range specified by Hengli for your specific machine and material.
Roller and drive system calibration: Ensure smooth operation of rollers and drive systems to prevent vibration.
5. Implement a regular maintenance protocol
Schedule routine lubrication of moving parts.
Clean blades, rollers, and tension systems regularly to prevent debris buildup.
Replace worn parts promptly to avoid instability during operation.
6. Monitor environmental conditions
Maintain optimal temperature and humidity levels for the production environment.
If external vibrations affect machine stability, take vibration mitigation measures.
Ensure proper grounding and electrical stability to prevent electric shock or power surges.
Advanced Techniques to Prevent Duplex Slitter Blowouts
· Use High-Quality Blades and Consumables.
To ensure consistent cutting performance and reduce the risk of material damage, invest in high-quality blades designed specifically for your material type. For example, Hengli blades are known for their durability, precision, and reliability, significantly reducing the likelihood of blades becoming dull, chipping, or breaking over time. High-quality consumables not only extend service life, but also minimize downtime due to frequent replacement or maintenance.
· Implement Real-Time Monitoring Systems
Integrating sensor-based monitoring systems into your slitting operations enables you to track key parameters such as tension, speed, and blade condition in real time. These systems immediately alert you when deviations occur, allowing operators to quickly make data-driven adjustments before problems escalate. This proactive approach helps maintain process stability and reduces the risk of blowouts or inconsistent cutting.
· Perform Material Testing and Quality Control
Before starting the slitting process, it is imperative to conduct comprehensive material testing to determine the optimal cutting parameters, such as tension settings and blade type. Additionally, regular quality control checks throughout the production process ensure material consistency and help detect any defects, impurities, or thickness variations that could affect slitting results.
· Upgrade to Advanced Slitting Technology
Modern slitters equipped with integrated automation and intelligent control systems can significantly improve production efficiency and accuracy. These systems can automatically adjust parameters such as tension and pressure in real time, minimize human error, and optimize performance for different material types and conditions. Upgrading to such technology not only improves cutting accuracy, but also improves overall safety and productivity.
· Hengli Is Committed to Providing Superior Slitting Machine Performance
Hengli is committed to providing advanced dual-station slitters equipped with advanced safety features, precise controls, and durable components. Our expert support team provides comprehensive troubleshooting assistance, customized maintenance plans, and training programs to ensure your operations are smooth and efficient.
Why Choose Hengli for Your Slitting Machine Needs?
- Innovative technology: Hengli slitters use cutting-edge technology to achieve optimal performance.
- Durability and reliability: Designed for demanding industrial environments.
- Expert support: Our technicians provide on-site and remote troubleshooting guidance.
- Customization: Customize solutions to meet your specific material and production requirements.
- Cost-effective maintenance: Reduce downtime and extend equipment life.
Conclusion: Achieve Optimal Performance with Troubleshooting from Hengli Experts
Solving the problem of double-station slitting machine bursting requires a comprehensive understanding of mechanical structure, material properties and best operating practices. Following the detailed troubleshooting steps above, manufacturers can significantly reduce downtime, improve cutting quality and extend machine life. Hengli is a professional silicon steel shearing equipment manufacturer. We are always committed to providing innovative solutions and expert support to help your business thrive in a competitive market.
Contact Hengli today to get personalized service, high-quality replacement parts and advanced equipment that meets the stringent requirements of your industry. We will serve you wholeheartedly to ensure that your double-sided slitting machine operates at maximum efficiency and consistently achieves high-quality cutting.
For can-making company to vertically and horizontally slit tinplate precisely.