How to Integrate a Blanking Line into an Existing Production Line
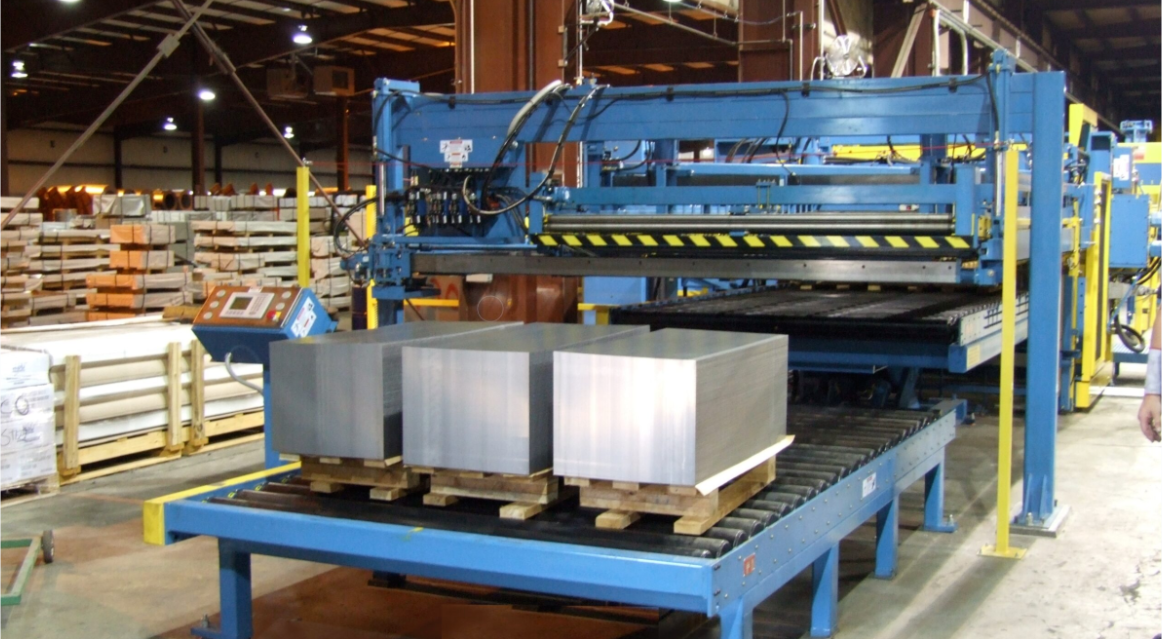
Integrating a blanking line into an existing production line is a strategic move that can improve operational efficiency, reduce waste, and improve product quality. At Hengli, we understand the complexities involved in such integrations and are committed to providing solutions that simplify this process. This comprehensive guide will take a deep dive into the necessary steps, considerations, and best practices for successfully integrating a blanking line into your production workflow.
What is a Blanking Line?
A blanking line is a production line that is specifically designed to cut flat sheet materials into specific shapes and sizes. The process is essential in industries such as automotive, aerospace, and electronics, where precision and consistency are paramount. The blanking process involves multiple stages, including feeding, cutting, and stacking, each of which requires careful planning and execution.
Benefits of Implementing a Blanking Line
Integrating a blanking line into your existing production setup can provide many benefits:
- Increased efficiency: Automating the blanking process reduces labor and speeds up production cycles.
- Reduce costs: Improving material utilization minimizes waste, resulting in significant cost savings.
- Enhanced quality control: Precision cutting ensures consistent product quality, reducing defects and rework.
- Flexibility: Blanking lines can accommodate a wide range of materials and designs, allowing for greater product diversity.
Evaluate Your Current Line
Before integrating a blanking line into your production process, it is critical to thoroughly evaluate your existing infrastructure. Key considerations include ensuring there is enough space to accommodate the new equipment without disrupting workflow, evaluating the compatibility of existing machines to determine if an upgrade is necessary, and assessing the skill level of your employees to ensure they can effectively operate and maintain the new line. Properly addressing these factors will help ensure a smooth integration and optimize production efficiency.
Determine Production Needs
Understanding your production needs is critical to successfully integrating a blanking line. Start by analyzing your production volume to determine the appropriate capacity for your line. Next, consider the type of material you will be blanking, as this will influence the choice of equipment. Finally, define your product specifications, including dimensions and tolerances, to ensure the blanking line can meet these exact requirements for consistent and accurate output.
Create a Detailed Integration Plan
A well-structured integration plan is essential to minimize disruption during the blanking line installation process. The plan should include a realistic timeline with key milestones to ensure timely completion, a comprehensive budget covering equipment costs, installation, training, and potential downtime, and a comprehensive risk assessment to identify possible challenges and outline mitigation strategies. Proper planning will help ensure that the integration process is smooth and efficient.
Choose the Right Equipment
Choosing the right blanking line is essential to achieving optimal performance in your production process. When evaluating options, focus on the machine's technical specifications, such as cutting speed, accuracy, and material compatibility, to ensure it meets your production needs. It's also important to choose a reputable manufacturer known for quality and reliability. Additionally, give priority to vendors that offer strong after-sales support, including maintenance and training, to ensure the long-term success and smooth operation of your equipment.
Prepare the Installation Site
Before installation begins, the site must be properly prepared to ensure a smooth process. This includes cleaning and tidying the installation area, removing any unnecessary equipment or materials that may hinder installation. Additionally, a thorough electrical and mechanical inspection is essential to confirm that all connections and systems are functioning properly and can support the new equipment. Proper site preparation helps avoid delays and ensure a seamless installation.
Installing a Blanking Line
The installation process of a blanking line should be conducted by an experienced technician to ensure proper setup and optimal performance. Critical steps in this process include assembling components according to the manufacturer's guidelines to ensure proper configuration, followed by calibration to confirm that the equipment is operating within the specified tolerances required for production needs. Finally, it is critical to thoroughly test the blanking line to identify and correct any potential issues before full production begins to ensure smooth and efficient operation.
Provide Comprehensive Training
Training employees includes operational training to provide operators with hands-on experience so they can effectively use the new equipment. Additionally, maintenance training is essential for personnel to understand routine maintenance and troubleshooting techniques, which will help minimize downtime. Additionally, it is important to ensure that all employees are familiar with safety protocols related to blanking line operations to foster a safe work environment and reduce the risk of accidents.
Regular Maintenance and Optimization
Ongoing maintenance is essential to ensure the longevity and efficiency of your blanking line. Implementing a routine maintenance program should include regular inspections to assess component wear and identify potential issues before they escalate. Additionally, performance evaluations through regular reviews of production data can help identify trends and identify areas that need optimization. This proactive approach will not only extend the life of the equipment, but also improve overall production efficiency and reliability.
Hengli - Your Most Reliable Blanking Line Manufacturer
Hengli is a dedicated blanking line manufacturer that focuses on the research and development of high-end industrial automation equipment. As a national high-tech enterprise, we are committed to providing cutting-edge solutions to meet the growing needs of modern industry. As one of the leading sheet metal cutting and forming automation equipment suppliers, our main product lines are synchronized with the world's most advanced technologies.
Our cutting-edge solutions are widely used in automotive manufacturing and parts processing, steel metallurgical processing, power generation and metal packaging. Our products play a key role in supporting the growth and efficiency of key industries and contribute to the development of the national economy. Hengli attaches great importance to innovation, quality and customer satisfaction, always standing at the forefront of industrial automation, providing reliable and advanced solutions to our valued customers. If you are looking to purchase a blanking line, please contact us.
Conclusion
Integrating a blanking line into an existing production line is a complex process that requires careful planning, execution and ongoing management. By following the steps outlined in this guide and working with a trusted supplier like Hengli, you can achieve seamless integration to increase your production capabilities. Take advantage of the blanking line and let your business achieve continued growth and success in the competitive manufacturing environment.