Frequently Asked Questions and Solutions for Cut-to-Length Cutting Production Lines
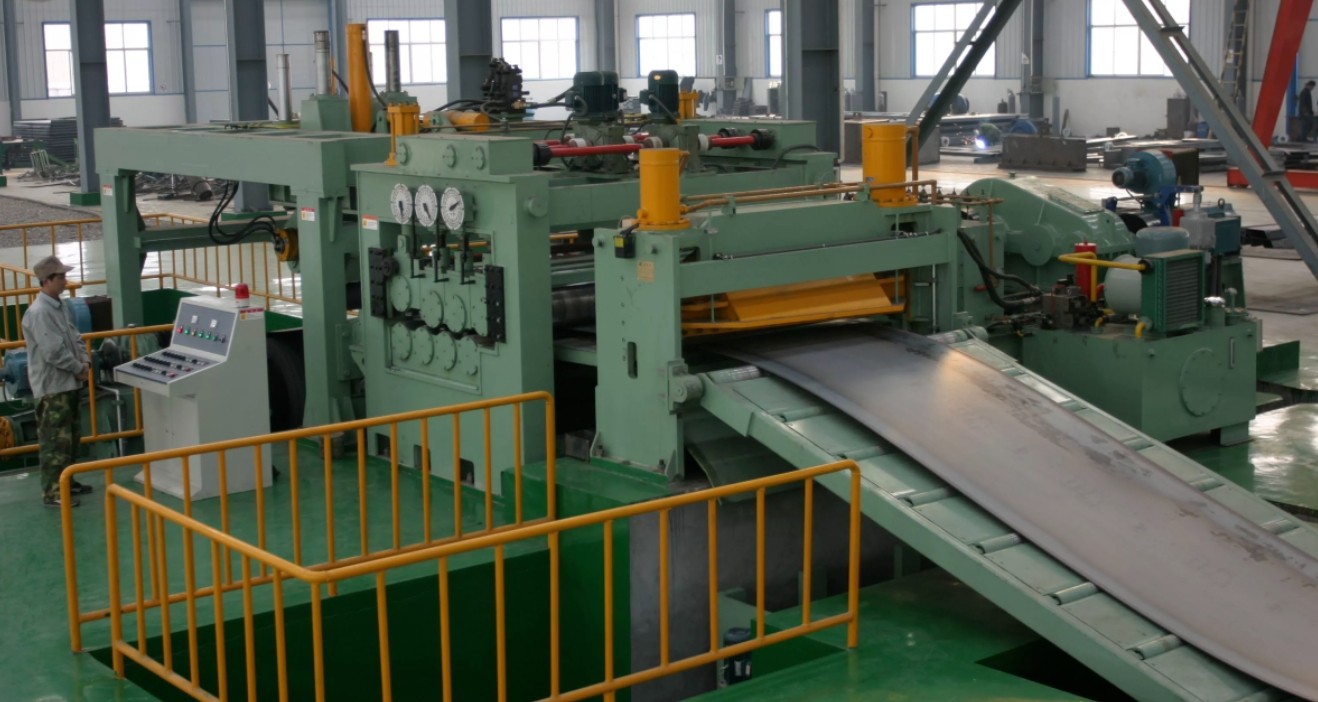
In the dynamic landscape of manufacturing, cut-to-length production lines play a key role in ensuring precise material dimensions for a variety of applications. From sheet metal to fabric, cut-to-length production lines greatly increase the efficiency of the production process. However, like any complex machinery, they are prone to common problems that can impact productivity. In this article, we'll take a closer look at these issues and explore practical solutions for keeping cut-to-length lines running seamlessly.
Definition of Cut-to-Length Cutting Line
In complex manufacturing areas, cut-to-length production lines become key components, coordinating the accuracy of material processing. These automated systems are designed to cut raw materials, from sheet metal to fabric, into predetermined lengths. The importance of cut-to-length lines lies in their ability to perform this task with unparalleled accuracy, laying the foundation for a seamless production process across different industries.
Cut-to-length lines are meticulous architects of material dimensions, ensuring uniformity and consistency that are vital in a manufacturing environment. By precisely defining the length of material, these production lines play a key role in minimizing waste, optimizing resource utilization, and ultimately increasing the overall efficiency of the production pipeline.
The Importance of Cut-to-Length Cutting Lines in Manufacturing
In a manufacturing industry where efficiency and accuracy are equally important, cut-to-length production lines have become unsung heroes. The streamlined precision they provide is indispensable, especially in areas where material dimensions directly impact the quality and functionality of the final product.
Whether it is the production of automotive parts, building materials, or textiles, the adaptability of cut-to-length lines makes them a versatile workhorse. Manufacturers rely on these systems to meet precise specifications, reduce operating costs, and improve output quality.
In essence, the cut-to-length collection is like a silent choreographer behind the scenes, orchestrating a harmonious dance of materials to ensure that each piece fits perfectly into the symphony of manufacturing.
Frequently Asked Questions About Cut-to-Length Cutting Lines
In the complex dance of defining precision and automation for cut-to-length production lines, some common issues can arise that pose challenges for manufacturers in different industries. Understanding and resolving these issues is critical to maintaining the efficiency and effectiveness of your cut-to-length production line. Let's delve into the most common problems faced by these automated systems:
A. Material Misalignment: A recurring challenge is material misalignment within cut-to-length lines. This can be caused by a variety of factors, including mechanical issues, irregularities in the input material, or inaccuracies in the positioning mechanism. Misalignment can lead to inaccurate cuts, wasting material, and disrupting a seamless production flow.
B. Inconsistent Cutting: Maintaining consistent cutting is critical for cut-to-length production lines. The dimensions of the material being cut may change due to factors such as blade wear, programming errors, or fluctuations in material properties. Inconsistent cuts not only affect the quality of the final product but can also lead to inefficiencies in the subsequent manufacturing process.
C. Equipment Downtime: Unplanned downtime is a significant issue for manufacturers that rely on cut-to-length lines for their production processes. Equipment malfunctions, malfunctions, and the need for routine maintenance can cause disruptions to manufacturing schedules, resulting in increased operating costs and delivery delays.
D. Quality Control Issues: Ensuring the quality of cut materials is an ongoing challenge for cut-to-length production lines. Dimensional deviations, defects, or irregularities in the cutting process can compromise the integrity of the final product. Quality control issues not only affect product quality but can also lead to increased scrap rates and customer dissatisfaction.
Solutions to Common Problems in Cut-to-Length Production Lines
Solving common problems faced by cut-to-length production lines requires a strategic approach and implementation of advanced solutions. Manufacturers can deploy a combination of technology and best practices to ensure seamless operation of cut-to-length production lines. Let's explore effective solutions to common challenges:
A. Advanced Alignment System: In order to solve the misalignment problem, it is crucial to adopt an advanced alignment system. Laser technology and computer control mechanisms can be integrated into cut-to-length production lines to ensure precise material positioning. These systems continuously monitor and adjust alignment, minimizing the risk of misalignment-related issues.
B. Precision Cutting Technology: Consistent and precise cuts are ensured by utilizing state-of-the-art cutting technology. For example, laser or waterjet cutting improves accuracy and reduces variation in cut dimensions. Manufacturers can upgrade their cut-to-length production lines with these advanced cutting technologies to optimize accuracy.
C. Regular Maintenance Practices: Proactive maintenance is key to preventing unplanned downtime. Implementing a regular maintenance program that includes thorough inspections and timely repairs can help identify and resolve potential problems before they escalate. This preventive approach minimizes the risk of equipment failure and increases the overall reliability of the cut-to-length production line.
D. Implement Quality Assurance Protocols: To address quality control issues, manufacturers can integrate strong quality assurance protocols into their cut-to-length production lines. Real-time monitoring and automatic inspection during the cutting process ensure the continuous production of high-quality materials. Implementing these protocols helps identify and correct defects, reducing the likelihood of damage to the final product.
E. Cost of Downtime: Recognizing the financial impact of downtime is critical. Manufacturers should invest in technologies and practices that minimize downtime, such as predictive maintenance tools that use data analytics and machine learning to predict potential problems before they occur.
F. Maintenance Cost: While scheduled maintenance incurs costs, it is a cost-effective strategy when compared to the financial losses caused by unplanned downtime. Manufacturers should view maintenance costs as an investment in the longevity and reliability of their cut-to-length production lines.
In Conclusion
In this comprehensive exploration of cut-to-length production lines, we take an in-depth look at prevalent challenges and effective solutions. Misalignment, inconsistent cuts, equipment downtime, and quality control issues are common problems. If you want to know more or want to purchase fixed-length cutting wire, please contact us.
Hengli As a professional cut-to-length cutting line manufacturer, we want to provide the right solution, one that is tailored to your specific business realities. We will listen carefully to your requirements and work with you to identify all aspects that need to be addressed, including materials, work, operator and packaging considerations. We specialize in providing reliable machines that increase your productivity, reduce waste and improve output quality. We also have more than 10 innovation patents and nearly 30 practical creation patents. As one of the national industry standard-setting members, we have core technologies and core products with independent intellectual property rights.
1. Leveler for high strength steel or aluminum
2. High precision digital level,
1.Suitable material:CRC,GI,EG, stainless coil
2.Material thickness:0.2 -3.0mm
3.Material width:400-1800mm